Ecowatch
Metal Waste Could Be Used as a Catalyst for More Sustainable Hydrogen Production, Researchers Say
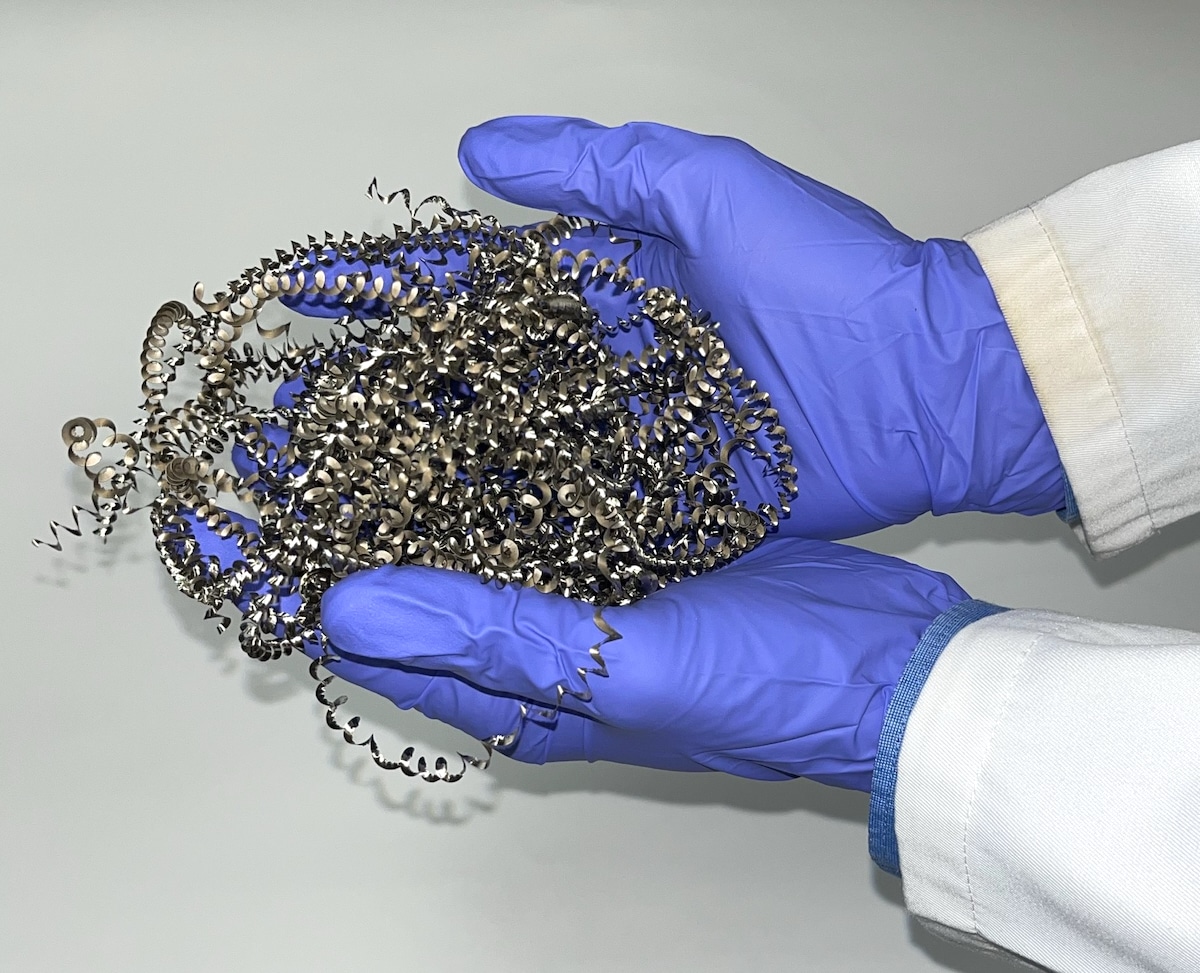
Swarf is a byproduct of the metal machining industry. University of Nottingham

Why you can trust us
Founded in 2005 as an Ohio-based environmental newspaper, EcoWatch is a digital platform dedicated to publishing quality, science-based content on environmental issues, causes, and solutions.
Researchers have found a way to reuse metal waste as an electrocatalyst that can split water (H2O) into hydrogen and oxygen, which could be help make hydrogen production more sustainable.
Hydrogen is considered a clean, renewable energy source, but the process to produce it often comes with a major carbon footprint. According to a 2021 study, the greenhouse gas emissions from blue hydrogen (hydrogen that is produced and followed by carbon capture and storage) can be 20% greater than natural gas or coal when used for heat, and the World Energy Council reported that 96% of hydrogen relies on fossil fuels for production as of 2019.
Scientists are therefore exploring ways to produce green hydrogen, or hydrogen produced via clean, renewable energy sources and electrolysis.
To investigate more sustainable methods of producing hydrogen, scientists from the University of Nottingham’s School of Chemistry and Faculty of Engineering tested the process of electrolysis using swarf, a metal machining byproduct, including stainless steel, titanium and nickel alloys as the waste materials.
They found that swarf has nanotextured surfaces with grooves that could help bond platinum or cobalt atoms. When bonded, they could lead to effective electrocatalysts which split water and produce hydrogen. The team shared their findings in the Journal of Material Chemistry A of the Royal Society of Chemistry.
“Industries in the UK alone generate millions of tons of metal waste annually,” Jesum Alves Fernandes, leader of the research team, said in a statement. “By using a scanning electron microscope, we were able to inspect the seemingly smooth surfaces of the stainless steel, titanium, or nickel alloy swarf. To our astonishment, we discovered that the surfaces had grooves and ridges that were only tens of nanometres wide. We realized that this nanotextured surface could present a unique opportunity for the fabrication of electrocatalysts.”
The team used magnetron sputtering, a method of physical vapor deposition, for 90 seconds to expose the swarf to platinum and cobalt atoms, which fit into the grooved surfaces of the swarf and reduced the amount of platinum or cobalt needed for splitting water.
The result is an electrolysis method of producing green hydrogen using metal waste while minimizing the cost and environmental impact related to the use of precious metals. Green hydrogen production can also minimize greenhouse gas emissions typically associated with producing hydrogen.
“It is remarkable that we are able to produce hydrogen from water using only a tenth of the amount of platinum loading compared to state-of-the-art commercial catalysts,” Madasamy Thangamuthu, postdoctoral researcher at the University of Nottingham, said in a statement. “By spreading just 28 micrograms of the precious metal over 1 cm² of the swarf, we were able to create a laboratory-scale electrolyser that operates with 100% efficiency and produces 0.5 litres of hydrogen gas per minute just from a single piece of swarf.”
The researchers have now partnered with AqSorption Ltd, an engineering firm based in Nottingham, to work toward scaling up the technology to produce green hydrogen.
Subscribe to get exclusive updates in our daily newsletter!
By signing up, you agree to the Terms of Use and Privacy Policy & to receive electronic communications from EcoWatch Media Group, which may include marketing promotions, advertisements and sponsored content.
Source
Disclaimer: No copyright infringement intended. All rights and credits reserved to respective owner(s).